10 Things to Know Before Methane Barrier Installation
Methane barrier installation is part of the overall methane mitigation construction process. Methane barrier construction in Los Angeles requires the use of specific materials with LADBS approval. Additionally, the applicator must have the proper certifications from the local building department and impervious vapor membrane manufacturers. In fact, each component of passive methane mitigation systems, as well as active methane mitigation systems, requires one or more professional licenses and certifications for this technical trade. Updated August 31, 2023.
10 Things to Know Before Methane Barrier Installation
1). A Methane Soil-Gas Survey (Methane Test) will be Required
This will determine the type of methane mitigation system that is required. It should be noted that the methane barrier is one of the core components of a methane mitigation system, along with the sub-slab piping and vent risers. Thus, if mitigation is required, you can be fairly certain that a methane barrier will be part of the design. But the methane test will determine the Site Design Level, which will outline what other components will be required, such as a methane gas detection and alarm system, for example. It is important to remember that for sites within the Los Angeles Methane Zone, even sites with no methane detected during testing, will require the installation of a methane barrier during construction.
2). A Methane Mitigation Plan will be Required
This is a separate plan that describes how the methane mitigation system will be installed. It includes the plan layout as well as product specifications and construction details. The Los Angeles Department of Building and Safety (LADBS) has published a generic “Standard Plan for Methane Hazard Mitigation”, which is available on the LADBS website. This Standard Plan may or may not be acceptable depending on the specific project. It calls for the most robust methane mitigation components without considering the specific details of the project. Oftentimes, a site-specific plan is required by the Building Department. This can be advantageous because it is based on the actual site conditions and may be able to streamline the process, making it more efficient. A custom methane mitigation plan must be designed by a qualified professional such as a licensed professional geologist experienced in methane mitigation design, as well as understanding the specific regulations of the local building department. Plan check by multiple departments can be expected (such as mechanical, plumbing, fire, etc.), and the methane mitigation designer should be able to assist with the submittal process.
3). A Methane Barrier is Not the Same as a Typical Vapor Barrier or Moisture Barrier
In fact, there is a limited number of products that meet the requirements for use as a methane barrier. This includes being approved by the LADBS Engineering Research Section with a valid Los Angeles Research Report (LARR) Number. And the installation of such a barrier must comply with the conditions of approval specified in a LARR and the manufacturer’s specification of the methane barrier. A contractor experienced in methane mitigation design and construction can help determine the best choice of methane barrier based on the specific project.
4). The Methane Barrier Must be Inspected Before the Slab is Poured
Methane Deputy Inspection is a service provided by a third party, on behalf of the Building Department. Your methane contractor can help to schedule the inspections at the appropriate times during construction. This is important to remember because timing the Deputy Inspections properly will help to keep a project on-schedule. Other departments will need to inspect different components of the mitigation system- for example, a Plumbing Inspector will inspect the sub-slab piping, and the Fire Department will inspect the methane gas detectors, but the methane barrier specifically will be inspected by the Methane Deputy Inspector.
5). Single-family residential projects may have different requirements from multi-family or commercial applications
This is important to know, because more efficient methods of methane mitigation may be possible. For example, certain projects may qualify for a simple visqueen barrier instead of a more robust (and expensive) barrier specifically certified for methane. This all depends on the results of the Methane Test. Along the same lines, there is a simplified method for small additions that is acceptable for projects not exceeding a certain size. These substitutions are legitimate and can help to keep a project’s budget more manageable, but it is important to understand the regulations in order to take advantage of these efficiencies. Your Methane Professional should be able to help you navigate the process of selecting the most-efficient pathway to compliance.
6). The Methane Barrier Must be Applied by an Approved Installer
Some general contractors may be certified to install certain methane membrane products. Or, they may sub-contract a methane professional to do the installation. Either way, it is important to confirm what product the methane contractor uses, and that it is an LARR-approved material. And, it is important to confirm which party is the certified applicator that will be installing the barrier.
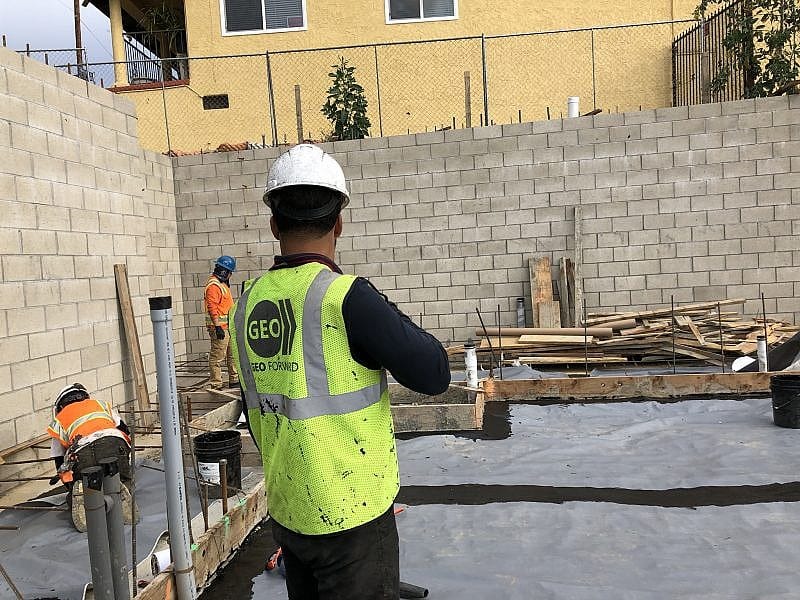
7). A methane barrier is not always required for construction projects in the Methane Zone or Methane Buffer Zone
Structures with raised-floor construction naturally ventilated buildings, and low-level Buffer Zone sites are all examples of projects which could potentially be exempt from the methane barrier requirement. However, this often depends on the results of the methane test. And, each of these examples has its own set of specific requirements for methane considerations, which still must be navigated during design and construction. An experienced methane professional should be able to determine the most efficient way to achieve compliance for a Methane Zone or Methane Buffer Zone construction project.
8). Know where to find additional information
It can be wise to read through the Los Angeles Building Department Methane Mitigation Standards. These documents provide information describing the installation procedures, design parameters, and test protocols for the methane gas mitigation system. The most informative and helpful of these documents are probably Ordinance No. 175790, and “Methane Mitigation Standard Notes.” Both can be found on the LADBS website.
9). The purpose of the methane barrier is to protect the health and safety of building occupants!
Methane gas in high concentrations is combustible. When subsurface methane gas accumulates under and around a building, it can create a fire hazard. In fact, a fire caused by methane in the Fairfax Area of Los Angeles in 1985, was the impetus to formalize the first Methane Ordinance in 1986. This is important to remember when considering the cost and complexity of methane site testing and mitigation. It is not simply a formality or the type of regulation that one should try to avoid. Rather, it is best to take seriously the requirements knowing that installing a proper methane mitigation system is everything a property owner can and must do to protect the health and safety of occupants.